Top 5 Reasons for Industrial Brake Failure - And How to Prevent Them
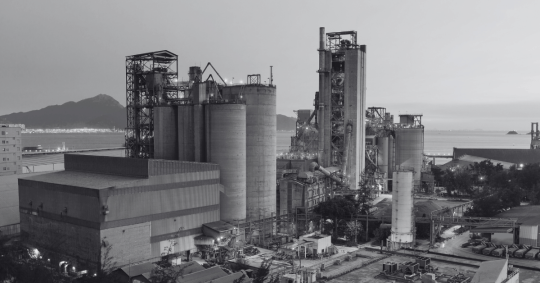
In industries like construction, agriculture, mining, ground care, and rail, your equipment’s braking system is one of the most important safety features. When brakes fail, it’s not just inconvenient, it can be dangerous and expensive. At Robert Cupitt, we’ve worked with businesses across the UK to supply industrial brake and power transmission components that are built to perform under pressure. Over the years, we’ve seen the same issues come up again and again when it comes to brake failure.
Understanding why brakes fail and how to prevent it can help you avoid costly repairs, unplanned downtime, and serious safety risks. Let’s explore the most common causes of industrial brake failure and what you can do to stay ahead of them.
Worn Brake Components That Go Unnoticed
One of the most common reasons for brake failure is simply worn-out components. Pads, discs, drums, and shoes naturally wear down with time and use, especially in heavy-duty machinery. When these parts get too thin, they lose the ability to create proper friction, which leads to longer stopping distances or total brake loss. Unfortunately, this kind of wear often goes unnoticed until performance starts to suffer or a breakdown occurs.
The best way to prevent this is with regular inspections. By checking brake thickness and surface condition during routine maintenance, you can spot early wear and replace parts before they fail. Keeping a service schedule helps ensure your brakes stay in peak condition year-round.
Overheating from Excessive Braking
Industrial machinery often operates in high-demand environments, like hauling heavy loads or working on steep terrain. Repeated braking under load creates heat, and if that heat builds up too much, it can cause serious damage. Overheating can lead to brake fade, where the brakes become less effective, or even cause components to warp or crack.
To prevent overheating, make sure your equipment is fitted with the right type of braking system for its workload. Disc brakes, for example, tend to handle heat better than drum brakes in high-performance settings. Choosing the right brake type, allowing time for cooling, and avoiding overuse of the brake system can all help reduce heat buildup.
Contamination from Dirt, Water, or Oil
Brakes are designed to operate in a clean and dry environment. When dirt, oil, water, or other contaminants enter the braking system, it can severely reduce friction and cause uneven or weak braking. In agriculture, mining, and ground care, where machines often work in muddy or wet conditions, contamination is a frequent cause of brake failure.
Proper sealing and regular cleaning are the best defences here. Make sure your brake system has protective covers where possible, and clean components during service checks. If your equipment frequently operates in wet or dusty areas, you may want to consider sealed drum brake systems or specially coated parts that offer better protection.
Hydraulic or Pneumatic System Leaks
In many industrial machines, braking relies on hydraulic or pneumatic pressure. Leaks in these systems, whether it’s a cracked hose, damaged seal, or worn-out master cylinder, can cause a sudden loss of pressure. Without enough force, the brakes may feel spongy, respond slowly, or fail completely.
You can prevent pressure loss by checking for fluid leaks or air pressure drops during regular maintenance. If a machine’s brakes feel soft or unresponsive, don’t ignore it. Investigate immediately, as this is often an early sign of a leak somewhere in the system.
Poor Installation or Incorrect Parts
Using the wrong parts or installing them improperly is another common reason for brake failure. Brake systems are carefully designed for specific loads, speeds, and environmental conditions. When incorrect components are used, they may not deliver the stopping power needed. Similarly, even high-quality parts can fail if they’re installed incorrectly or not adjusted properly.
That’s why it’s important to work with a trusted supplier like Robert Cupitt. We don’t just provide parts, we help you choose the right ones. Our team understands the demands of your industry and can recommend braking solutions that fit your equipment perfectly. Professional installation and proper setup ensure that your brake system performs as it should from day one.
Stay Ahead of Brake Failure with Robert Cupitt
Brakes may not always be the most visible part of your equipment, but they’re one of the most vital. Most cases of brake failure are preventable with the right combination of regular maintenance, proper component selection, and early detection. If your brakes are showing signs of wear, overheating, or unresponsiveness, now’s the time to take action, not after something goes wrong.
At Robert Cupitt, we specialise in supplying reliable, long-lasting brake components for industrial applications across the UK. Whether you work in agriculture, construction, mining, rail, or ground care, we’re here to help you find the best braking solution for your equipment and keep it running safely and smoothly.
Need help diagnosing brake issues or finding replacement parts?
Get in touch with Robert Cupitt today for expert advice and industrial-grade brake components built to handle the toughest jobs.
Need help finding the right solution?
Our experienced team is here to provide expert advice and help you choose the perfect component for your application. Contact us today to discuss your requirements.