Choosing the Right Brake System for Mining Equipment in Harsh Environments
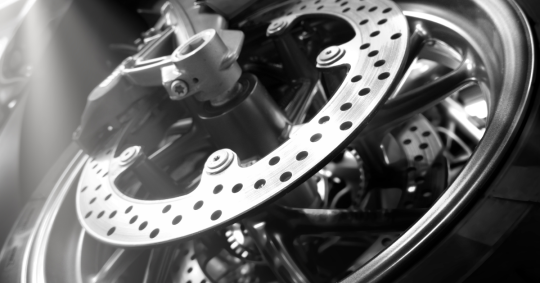
When it comes to mining, few things are easy on equipment. Machines are pushed to their limits every day, operating in dust, mud, heat and heavy loads. In these conditions, your brake system is more than a safety feature. It’s a lifeline.
The right brake system will improve control, extend service life and reduce downtime. The wrong one? That can lead to poor performance, faster wear and serious safety risks. If you're running or maintaining mining equipment in the UK or beyond, here’s what you need to know about choosing the right brakes for the job.
Why Brake Choice Matters in Mining
Brakes on mining equipment face tough conditions. These machines are large, powerful and often operate on unstable ground or steep grades. That means your brake system needs to be:
- Durable, withstanding shock loads and constant use
- Reliable, even in wet, dirty or abrasive environments
- Powerful, capable of stopping heavy loads on demand
- Serviceable, easy to maintain with minimal downtime
Whether you’re dealing with underground loaders, haul trucks, drills or conveyors, every system depends on the right brakes to keep operators safe and equipment in check.
Types of Brake Systems in Mining
There’s no one-size-fits-all solution. Here are the main types of mining equipment brakes and what they’re best suited for:
1. Wet Disc Brakes
These are sealed systems where the braking action takes place in oil. They offer smooth performance, better heat dissipation and longer life.
- Ideal for: Underground loaders, articulated dump trucks
- Benefits: Low wear rate, sealed from dirt and moisture
- Watch for: Oil contamination, seal failure, overheating
2. Dry Disc Brakes
Dry disc systems are exposed to the environment but offer high braking force and easier access for maintenance. They are more prone to wear in dusty or wet conditions, so routine checks are key.
- Ideal for: Surface haul trucks, large earthmovers
- Benefits: Simple design, strong stopping power
- Watch for: Dust build-up, pad wear, vibration
3. Drum Brakes
Still used in some equipment, drum brakes are enclosed and can work well in controlled settings. But they don’t cool as efficiently as disc brakes, which can be a drawback on steep terrain or in high-speed operations.
- Ideal for: Older machinery, low-speed conveyors
- Benefits: Enclosed system, cost-effective
- Watch for: Heat build-up, liner wear, sluggish response
4. Spring-Applied Hydraulic Release (SAHR) Brakes
These fail-safe brakes engage automatically if hydraulic pressure is lost, making them ideal for mining safety systems. They are often used in parking or emergency brakes on large machines.
- Ideal for: Loaders, drills, longwall machinery
- Benefits: Reliable, safety-first design
- Watch for: Seal wear, pressure loss, internal corrosion
Key Factors When Choosing a Brake System
To make the right choice, think beyond brake type. These are the key factors to consider:
Operating Environment
Dust, water and temperature extremes all affect brake performance. Wet brakes are better in underground or slurry-heavy environments. Dry brakes may work better in drier, surface operations where maintenance is easier.
Machine Load and Speed
The heavier or faster the equipment, the more stopping power you need. Overspecify the brakes if there’s any doubt; safety and control should always come first.
Maintenance Capacity
If you’re in a remote location or running with a small team, choose a brake system with longer service intervals and simpler repairs. Wet disc systems often win here, but some dry systems are easier to swap out when needed.
Regulatory Standards
In the UK and elsewhere, mining operations must follow strict safety rules. Always check that brake systems meet local standards, especially for critical applications like manned vehicles or load-bearing machinery.
When to Upgrade or Replace
Even the best brakes wear out. Watch for these signs:
- Reduced stopping power
- Squealing or grinding noises
- Excessive heat after braking
- Warning lights or sensor alerts
- Leaking hydraulic fluid or brake oil
Regular inspections and preventative maintenance are essential. In mining, delays can be costly. So when in doubt, don’t wait. Replace early rather than risk a breakdown.
Why Robert Cupitt?
If you’re sourcing heavy-duty brakes in the UK or need help with mining power transmission, we’re here to help. At Robert Cupitt, we supply mining equipment brakes for all types of machinery, from OEM-standard replacements to specialist upgrades for extreme-duty use.
We work with trusted global brands and can advise on systems for both surface and underground operations. Whether you need a quick turnaround or want to future-proof your fleet, get in touch with our team.
Final Word
The right brake system doesn’t just slow you down, it keeps everything moving safely. In mining, where every day and every load counts, your brakes need to be as tough as your equipment.
If you’re not sure what system your machinery needs, or want to upgrade for better performance and safety, we’re happy to help. With decades of experience in harsh environment braking, we’ll make sure you get the right part, the first time.
Need help finding the right solution?
Our experienced team is here to provide expert advice and help you choose the perfect component for your application. Contact us today to discuss your requirements.